Patient safety and health
Patient safety and health is a top priority for Galenica. Galenica is committed to ensuring the quality of medicines along the entire value chain.
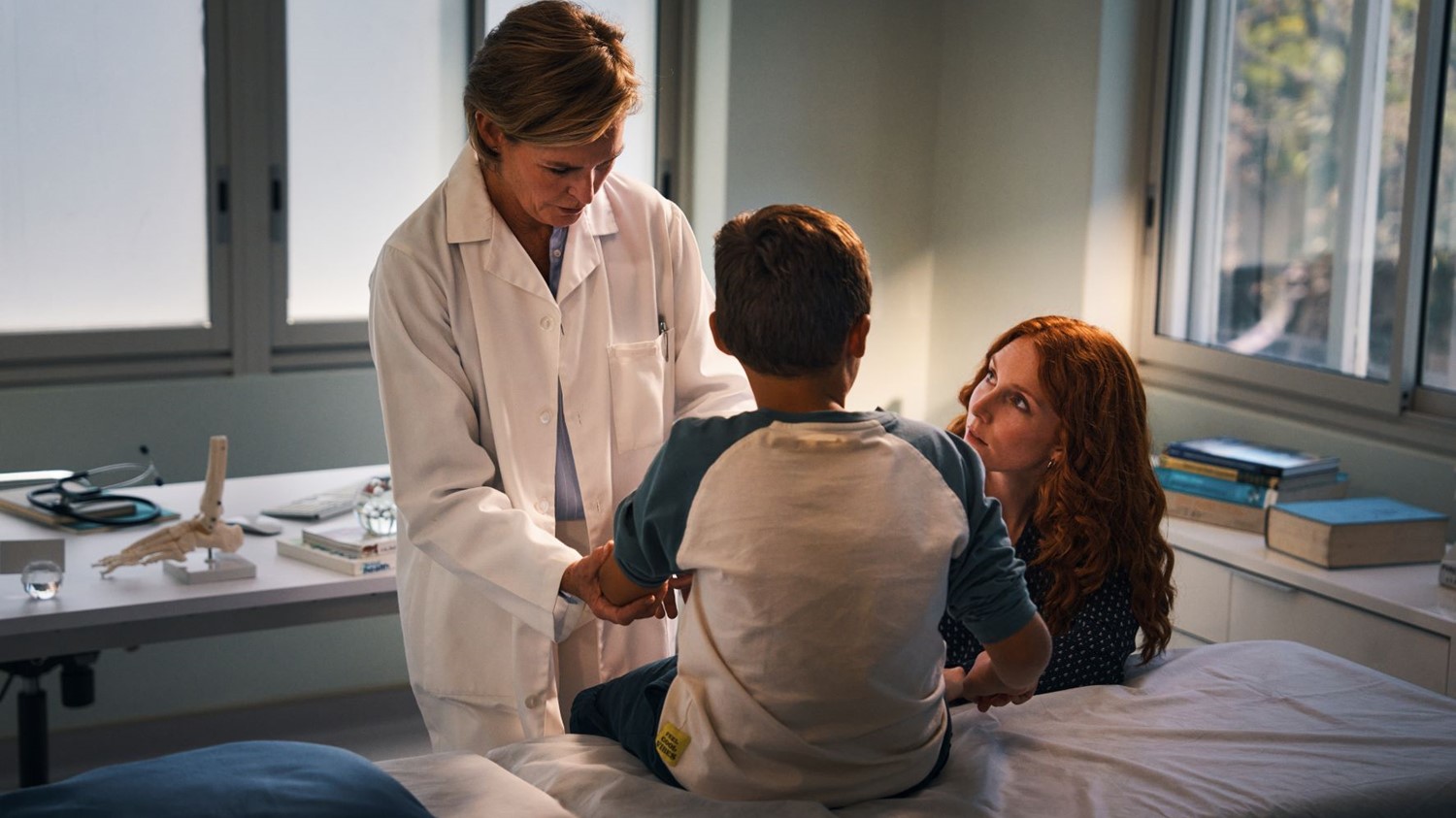
Own material topic
Patient safety and health
GRI 3-3
Management of material topics
Medication errors or reductions in the quality of medications can have serious consequences for a patient’s health. They also pose a reputational risk for the companies involved. Digitalisation opens up new opportunities for innovative solutions to improve patient safety. Galenica is committed to ensuring the quality of medicines along its entire value chain and takes the appropriate measures along the supply chain in terms of infrastructure, processes, and employee training and education. With personal and competent advice and a unique range of products and services, Galenica supports its patients in all life situations and helps people of all ages lead a healthy life. Galenica thus makes an important contribution to the well-being and health of the Swiss population.
Objectives
Galenica has defined the following objectives:
- We will increase the use of Clinical Decision Support Checks (CDS.CE) to 500 million by 2025 and 1 billion by 2030 (base year: 2021).
- We will make patient information on all Algifor® preparations and important cold products from Verfora available online in two additional languages that are relevant for Switzerland by 2022.
Galenica has also defined internal objectives in the area of patient safety and health.
You can find an overview of all sustainability goals and the progress made here.
GDP guidelines for a good distribution practice
Alloga, Galexis, UFD, Pharmapool, Verfora and the Bichsel Group adhere to the GDP guidelines for human medicinal products in an exemplary manner. On the one hand, these legal requirements are intended to prevent counterfeit drugs from entering legal supply chains. On the other hand, control measures within the distribution chain ensure the quality and integrity of drugs. Drug temperature is recorded and analysed in real time throughout the entire life cycle, from production through to delivery to the customer. If there are deviations in temperature, the causes are investigated and suitable measures are taken in accordance with GDP guidelines. In addition to these guidelines, the aforementioned companies apply their own standards and processes in their day-to-day work to ensure patient safety at all times.
Galexis, UFD, Pharmapool and the Bichsel Group each operate their own fleet comprising 164 delivery vans (up to 3.5 tonnes) and 5 lorries (14 to 22 tonnes). All vehicles are GDP-compliant and are fitted with an air conditioning system in the loading space, which is mandatory for the transport of pharmaceutical products.
Quality systems
HCI Solutions provides master data for the Swiss healthcare market. The company is also active in the field of e-health with the aim of increasing patient and medication safety in the Swiss healthcare system. With innovative digital solutions such as Documedis®, HCI Solutions makes a significant contribution to safe and efficient healthcare in Switzerland. To guarantee the quality of medication data, HCI Solutions carries out process-integrated checks. The company checks the acquisition of drug data according to the four-eyes principle, while the six-eyes principle applies to sensitive active substances (such as blood thinners). HCI Solutions carries out random quality checks on a daily basis and a more comprehensive inspection every two weeks. Any error discovered is documented and its cause investigated. HCI Solutions is certified to ISO 9001:2015 and ISO 13485:2016.
The QMS of the Service Unit Pharmacies has standard operating procedures (SOPs) for all relevant pharmacy processes. These include the manufacture and dispensing of drugs, data protection, confidentiality, hygiene and the disposal of medications. Galenicare regularly carries out audits to ensure compliance with the SOPs in the individual pharmacies. In addition to these announced audits, anonymous test purchases and phone calls and inspections by cantonal pharmacists take place in all pharmacies. Several times a year, Galenica conducts QMS and legal requirements courses for pharmacy employees. For specific services such as heart checks, allergy checks, diabetes checks and vaccinations, employees complete certified courses and obtain certificates of competence.
As a company specialising in pharmaceutical manufacturing and home care with its own certified general pharmacist, the Bichsel Group places great importance on the quality of its products and services. The company carries out numerous chemical and microbiological analyses on a daily basis to check end products, raw materials and packaging materials and holds manufacturing licenses, EU GMP certificates for medicinal products and EC certificates for medical devices in accordance with Directive 93/42/EEC of the European Council.
The specialty pharmacy Mediservice supports patients with chronic and rare illnesses by providing additional services such as home care and patient events. Mediservice also has a licence to operate as a public pharmacy and a wholesale licence. Accordingly, Mediservice’s QMS meets a wide range of requirements.
For more information on certifications and quality systems, please refer to Compliance (GRI 419).
Continuous monitoring of all products
Product safety is checked and safeguarded at Verfora using a variety of approaches. Verfora checks that contract manufacturers qualify for the necessary processes by carrying out initial and regularly recurring audits. These evaluate compliance with the GMP guidelines and ensure that they are adhered to so that safe products can be manufactured for patients at all times. The audits also take into account environmental, health and safety factors within the partner companies. The products are then carefully examined before being placed on the market to ensure that they have been manufactured and tested in accordance with the GMP guidelines and that they meet all applicable specifications. As with all medications, Verfora products undergo a preclinical and a clinical trial to ensure their safety and efficacy. Once the products are on the market, pharmacovigilance is at the heart of Verfora’s safety efforts, i.e. the continuous monitoring of all products. All new Verfora employees are trained in pharmacovigilance and receive a checklist of steps to be taken in the event of side effects. In addition, pharmacovigilance training is held for all employees every year. The company also systematically checks advertisements and advertising posters for products to ensure they are correct. In parallel to pharmacovigilance, the products are regularly analysed in the laboratory until the end of their life so that any deviations in quality can be identified and remedied at an early stage.
Promote the technical competence of employees
In 2022, around 115 pharmacists attended quality management courses. Quality management and patient safety are also key issues in the basic training of pharmacy assistants working towards their Federal Proficiency Certificate.
Where required, Verfora offers training sessions for pharmacies when new medications are launched in order to promote employees’ skills and ensure patient safety and health. In 2022, Verfora conducted 150 training sessions for a total of 7,670 pharmacy assistants and pharmacists.
Increased patient safety using e-medication solution
Digitalisation is leading to new, innovative ways to improve patient safety. Documedis® is the process-integrated solution for increased medication and patient safety in the healthcare system. Documedis® offers specific e-health applications and services relating to the medication process based on INDEX data. HCI Solutions works with various reference communities to make Documedis® available in the electronic patient record. This will allow more functions to be made available to the various service providers in the future, such as merging several e-Mediplans , which will result in an increase in patient safety. Documedis® is already being implemented in pharmacy, medical and hospital software.
The Documedis® module Primary Care Algorithms (PCA.CE) provides the option of offering precise identification of health disorders and illnesses using algorithms. There are 33 algorithms in total. Documedis® also includes Clinical Decision Support Checks (CDS.CE Check). These checks enable pharmacists to check the patient’s used or planned medication for known risks, duplication or allergies to active substances. There are currently 13 such CDS.CE checks. The CDS.CE Check thus supports service providers when prescribing new medications or when supplementing existing medication. HCI Solutions is continuously expanding the functionality of Documedis®. Documedis® Vaccination will also be available in the course of 2023. Documedis® Vaccination is the new digital all-in-one solution for vaccination: from vaccination documentation and analysis to the creation of a clear vaccination plan.
Uninterrupted cold chain for medications
All Wholesale & Logistics companies, as well as Medifilm, Mediservice and Bichsel, provide an uninterrupted cold chain for the storage and transport of temperature-sensitive drugs. At Alloga, this also applies to so-called ultra-deep-freeze logistics, in other words, storage and dispatch at –80°C, the required temperature for a new generation of cancer drugs. In preparation for the delivery of COVID-19 vaccines, Alloga further expanded its ultra-deep-freeze logistics in the reporting year. Temperature control is ensured by using dry ice in special containers. Alloga and Galexis also use paraffin-filled cooling elements, which, in contrast to water-based cooling elements, ensure the medicines remain at a more stable temperature. The proportion of transported refrigerated products in the reporting year was 6% for Galexis’ own vehicle fleet and around 31% for third-party transport.
Important contribution to combating the coronavirus
Galenica pharmacies are making an important contribution to combating the coronavirus. From mid-November 2020, the first of them offered both rapid antigen tests and PCR tests for coronavirus, and pharmacies have also been offering COVID-19 vaccinations since 2021. In 2022, Galenica pharmacies carried out around 88,000 antigen, PCR and antibody tests and administered over 47,000 COVID-19 vaccinations.
Evaluation of the management approach and measures
- Quality management: the QMSs of the companies of the Galenica Group are regularly and systematically audited.
- GDP guidelines: the regional therapeutic products institutes periodically check compliance with the GDP guidelines.
- Pharmacovigilance: at Verfora, all employees are obliged to forward reports of side effects from specialists and patients to the responsible internal office promptly and in full. Information on the duration, progression and impact of the side effect and on the dosage and duration of product use plays a key role in this. Verfora documents and investigates each report, taking appropriate measures where necessary.
Own indicator
Pharmacovigilance: forwarding reports
In 2022, Verfora employees met the deadline for forwarding reports of side effects in 98% of cases (target: >90%). At Bichsel, the responsible parties met the deadline for forwarding reports of side effects to the authorities in 100% of cases.
Own indicator
QMS training in pharmacies
In the reporting year, 115 pharmacists completed QMS training.