Reliable procurement and supply chain
Delivery shortfalls in the pharmaceutical supply chain are increasing all over the world including in Switzerland. As a leading fully integrated healthcare service provider, we are increasingly attaching importance to reliable procurement and supplies of medications for the general population.
Our approach to this matter
The reasons for the shortfalls along the supply chain include centralised production at only a small number of sites around the world as well as outages or quality problems in the value chain. As a leading fully integrated healthcare service provider, Galenica is dependent on manufacturers’ delivery capabilities. It works closely with suppliers to ensure the highest possible availability of medications. Thanks to harmonised processes, suppliers provide information of any possible delivery delays in good time. In addition, an IT-based materials management system helps Galenica to optimise its procurement and logistics processes. The current COVID-19 pandemic has additionally heightened the relevance of reliable procurement and supplies.
Facts and figures
Early response to critical shortfalls
The Galenica Group’s logistics companies check warehouse supplies of pharmaceuticals on a daily basis and, in this way, are able to respond in good time to any shortfalls and peaks in demand. The average availability of medications stands at 99.6%. In the event of any critical shortfalls of the type that repeatedly occurred in 2020 on account of the COVID-19 pandemic, the logistics companies adjust their operations swiftly. In this case, deliveries of non-essential products such as cosmetics or perfume products are temporarily suspended and order quantities per customer reduced to prevent hoarding. During the first phase of the pandemic, trained administration staff were additionally assigned to the warehouse as crisis assistants to cope with the large volumes.
Non-pharmaceuticals strengthened
The coronavirus pandemic triggered increased demand for articles such as disinfectants, face coverings and disposable gloves. As a result, the distribution service providers expanded their non-pharmaceutical activities significantly in 2020. Employees were required to assess the quality of products sourced from new suppliers within a short space of time. Our companies rolled out efficient and reliable quality assessment processes and broadened employees’ knowledge by means of specific training. The authorities indicated that doctors and pharmacies must also maintain compulsory pandemic inventories of products, including gloves, disinfectant and face coverings. As of 2020, Galexis has offered to manage these inventories, resulting in synergy gains and economies of scale for customers.
Outlook for 2021
To continue ensuring the highest possible availability of medications in the future, Galenica will be expanding its order management system as well as the warehouse capacity at its Niederbipp site in 2021. Initial planning was completed in 2020. Working with an external service provider, Galexis developed a plan for the order management system to ensure that shortfalls can be identified even more effectively in the future in conjunction with the suppliers.
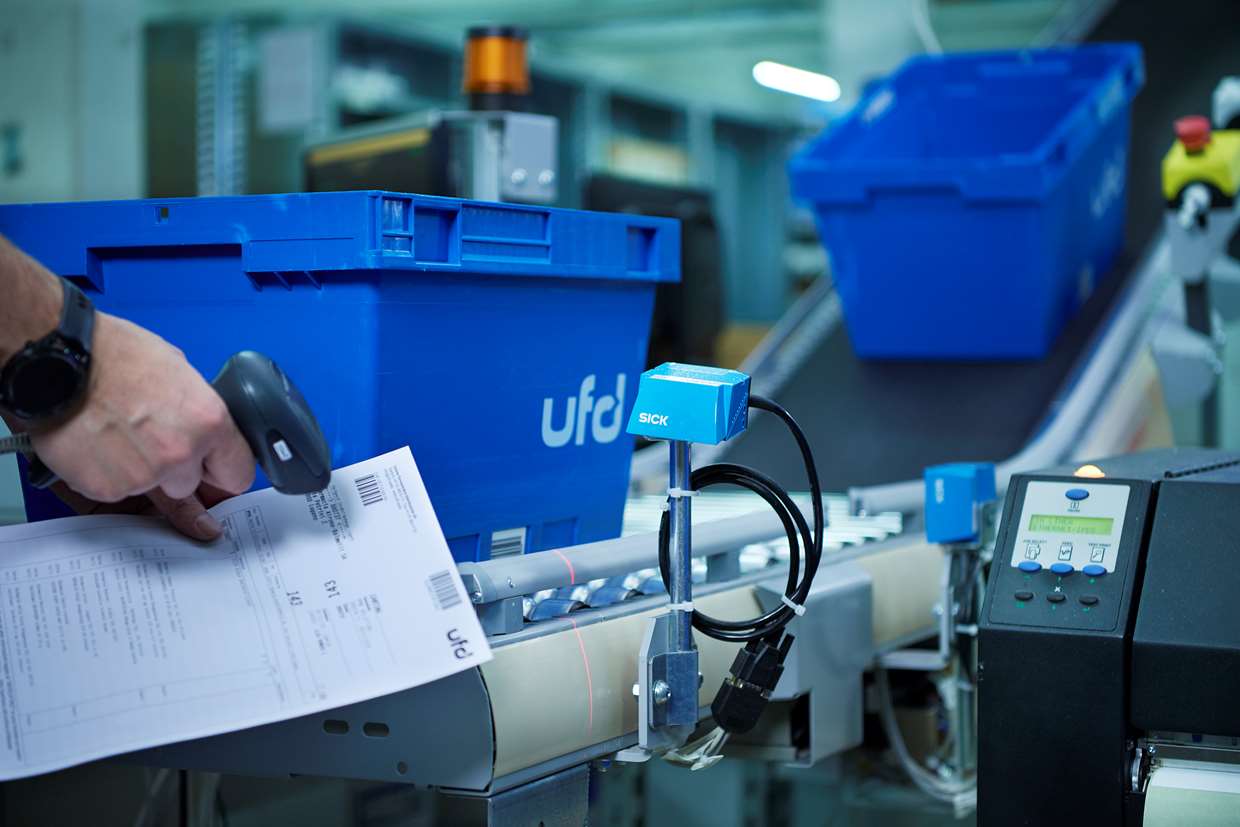